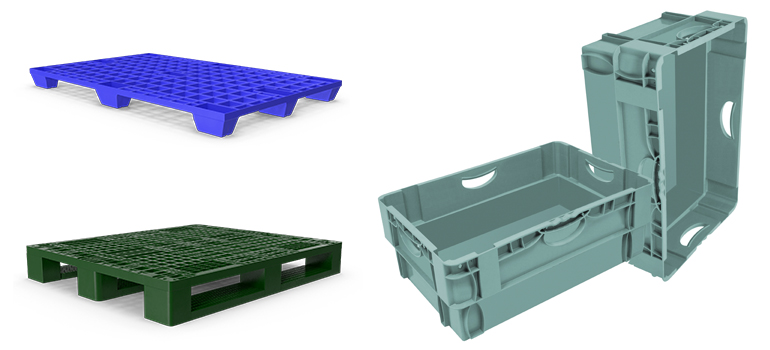
LEAN and Green – Reusable Totes, Bins, and Containers Impact Manufacturer’s Environmental Footprint as well as their Bottom Line
- Using reusable containers for shipping and production is ‘green’ and less expensive over time than disposable containers.
- Radio Frequency Identification (RFID) Technology allows automatic tracking of reusable containers
- Tracking provides accurate management of mission-critical parts during production
- Companies can verify which containers were shipped and to whom
Every day around the world companies ship, transport, move, carry, deliver, or receive things. The cardboard, paper, plastic and other materials used to transport these things from here to there are often disposable and much of it ends up in the landfill. In addition to having a significant influence on a company’s finances as a resource that must be continually replenished, disposable containers impact their carbon footprint and ecological impact at a time when companies are actively striving to be good environmental citizens. The use of reusable totes, bins, pallets, gaylords, and other containers is growing at a rapid rate as companies continue to look for ways to reduce both their expenses and environmental impact. A reusable container saves money over time, but it becomes necessary to track them to fully take advantage of this savings. Tracking prevents loss and ensures the return or the reusable containers but also creates a whole new avenue to create LEAN efficiencies and gather business data as tracking of the containers allows the tracking of the tools, parts, materials or products that they contain. Manual tracking often proves too labor intensive. By using a technology-based solution, such as RFID or barcode, manufacturers can achieve increased performance, eliminate confusion and downtime but avoid the additional labor costs that are required with manual tracking.
RFID allows you to automatically track these items throughout your manufacturing cycle. As a tote, bin or container moves through your processes it can be automatically tracked providing accurate management of mission-critical parts to keep your work flowing as well as supporting LEAN initiatives to identify bottlenecks and other problem areas in your processes. This same technology is also used to verify which containers were shipped and to whom. This data is stored in a data base so you can track where your assets are in your supply chain and also begin to mine the data for insights into your production process.